Available Sizes:Standard and custom sizes available upon request
Product Applications:Used in electroplating, chemical, and marine industries
Processing Technology:Explosive bonding and hot-rolled processing techniques
Quality Control and Testing: Strict testing ensures adherence to ISO9001-2000, PED, ABS standards
Product Implementation Standards:ASME, ASTM, JIS certified
Delivery:Available via sea, air, and express shipping
Packaging:Secure wooden crates for international transport
Product Introduction
The copper clad aluminum plate is a composite material that combines the advantages of both copper and aluminum. Using advanced explosion bonding or roll bonding techniques, the product offers superior conductivity, corrosion resistance, and durability, making it an ideal choice for applications across various industries. With a lightweight aluminum base and a high-conductivity copper cladding, this material is cost-effective while ensuring excellent performance.
Product Specifications
Cladding Material | Copper (C11000, T2) |
---|---|
Base Material | Aluminum (1050, 1060, 3003) |
Cladding Size | Customizable |
Cladding Technology | Explosion Bonding or Roll Bonding |
Product Standards | GB/GBT, ASME/ASTM, JIS |
Thickness | 2mm - 50mm (customizable) |
Length | Up to 6000mm |
Width | Up to 2500mm |
Surface Treatment | Polished, Matte, Brushed |
Packaging | Wooden crates, moisture-proof wrapping |
Delivery Cycle | 3-6 months or negotiable |
![]() |
![]() |
![]() |
![]() |
Copper-Aluminum Cladding Methods
Copper-aluminum clad plates combine the best properties of copper and aluminum, making them an ideal solution for industries where both conductivity and light weight are essential. The process of creating these composite materials involves advanced bonding techniques that fuse copper and aluminum together, ensuring superior mechanical and electrical properties.
Explosive Bonding
Explosive bonding is a high-energy method in which an explosive charge is used to bring copper and aluminum together with extreme force. This violent impact results in a metallurgical bond between the metals, ensuring a durable and effective connection.
Preparation: Copper and aluminum layers are cleaned and positioned, ensuring proper alignment before detonation.
Explosion Impact: The explosion generates a high-speed collision between the two layers, forming a strong bond.
End Result: The bond created through this process ensures a robust connection that can withstand high mechanical stress and corrosion.
Explosive bonding is typically applied in situations that require high-strength bonds, such as in the production of electrical equipment, heat exchangers, and pressure vessels.
Roll Bonding
Roll bonding is a cold-welding method in which copper and aluminum sheets are passed through heavy rollers under high pressure. The force applied by the rollers creates a strong bond between the two materials without the need for heat.
Preparation: Both copper and aluminum are carefully cleaned to remove any contaminants that may affect the bonding process.
Rolling Process: The materials are fed through rollers under pressure, and multiple passes may be necessary to ensure a complete bond.
Outcome: The result is a tightly bonded copper-aluminum composite that combines the conductivity of copper with the lightness of aluminum.
Roll bonding is often used to create materials for industrial applications such as electrical conductors, automotive parts, and chemical processing equipment.
Hot Isostatic Pressing (HIP)
Hot Isostatic Pressing (HIP) involves placing copper and aluminum inside a sealed chamber, where high temperature and pressure are applied. The process ensures a diffusion bond between the materials, resulting in a strong and uniform connection.
Sealing and Encapsulation: Copper and aluminum are placed inside a chamber and sealed to maintain the desired conditions.
Heating and Pressurization: The sealed chamber is subjected to extreme heat and pressure, allowing the metals to bond on an atomic level.
End Result: The bond formed by HIP ensures high structural integrity and excellent performance under challenging conditions.
HIP is particularly useful in applications requiring materials with superior bonding strength and integrity, such as in aerospace, power generation, and specialized industrial components.
Key Features and Advantages
Corrosion Resistance
Copper-aluminum clad plates exhibit excellent resistance to corrosion, especially in marine and chemical environments. The copper layer offers protection against corrosion, while the aluminum provides structural support, making the material highly durable.
Electrical Conductivity
The copper layer ensures superior electrical conductivity, which is essential in electrical and electronic applications. This makes copper-aluminum clad plates ideal for use in components such as busbars, connectors, and other electrical systems.
Lightweight
Aluminum is known for its light weight, which makes copper-aluminum clad plates a perfect solution for industries that need materials that are both strong and lightweight. This makes them suitable for use in aerospace and automotive applications where reducing weight without compromising performance is critical.
Durability
Combining copper's strength and aluminum's light weight, copper-aluminum clad plates provide enhanced durability. The material is resistant to wear, corrosion, and other environmental stresses, ensuring longevity and reliability in demanding applications.
Cost-Effective
By using aluminum, which is more affordable than pure copper, copper-aluminum clad plates offer a cost-effective alternative to solid copper. This makes them an economical choice for a wide range of industries without sacrificing performance.
Thermal Conductivity
Copper is known for its excellent thermal conductivity, making copper-aluminum clad plates an ideal material for applications requiring efficient heat dissipation. These materials are commonly used in heat exchangers, radiators, and cooling systems.
Customizability
Copper-aluminum clad plates can be customized to meet specific requirements in terms of thickness, size, surface treatments, and material ratios. This flexibility allows for tailored solutions across various industries.
Explosive Composite Panel Production Site
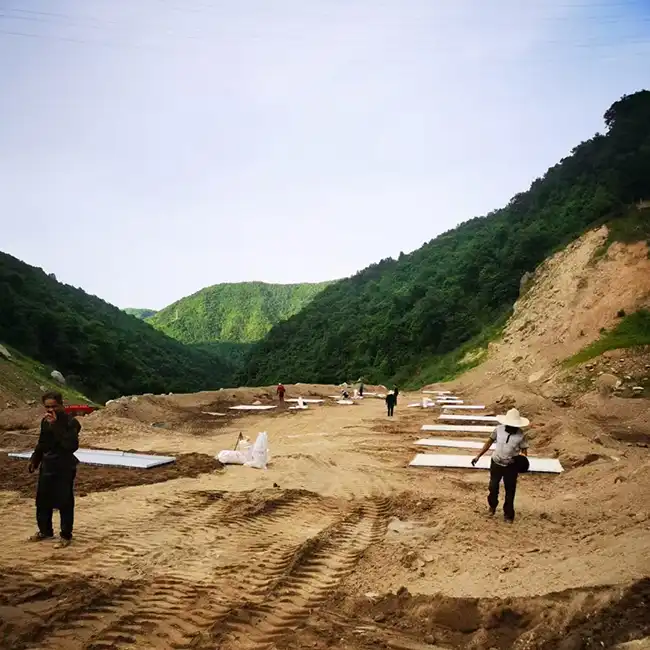
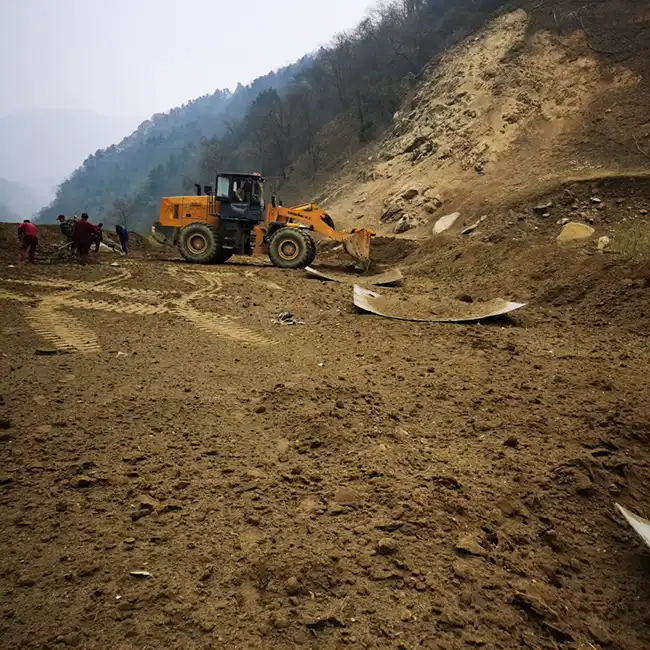
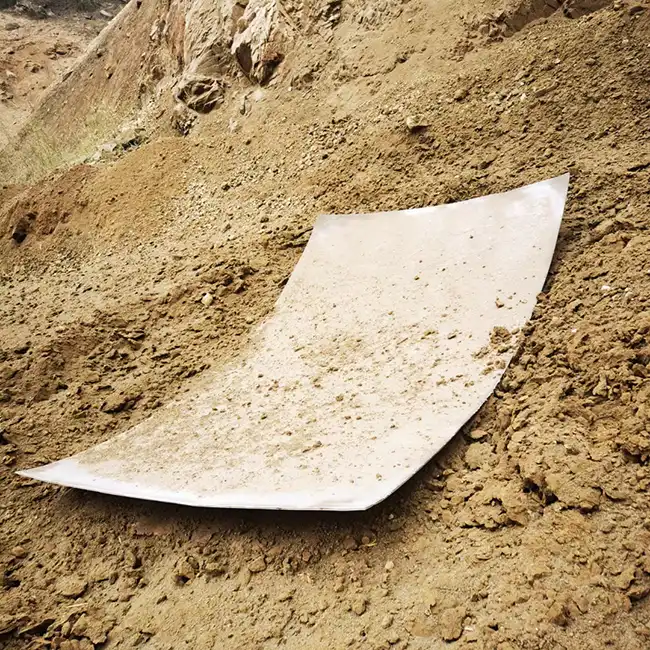
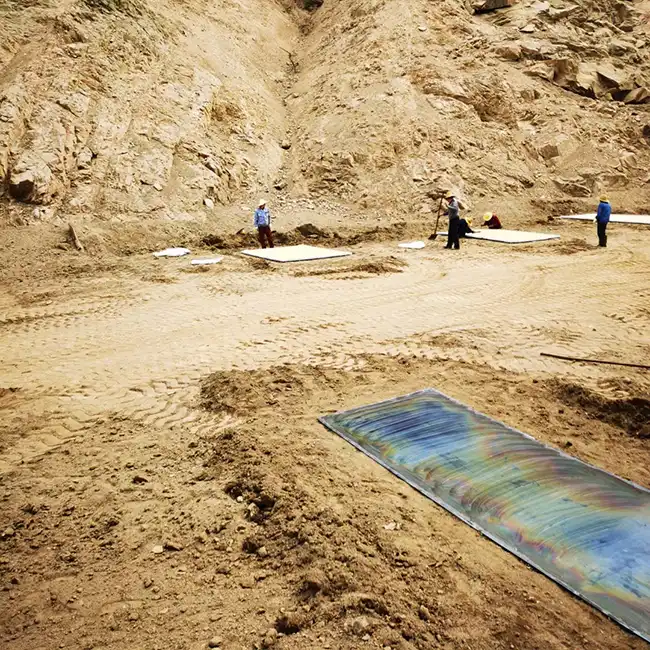
Explosion Welding Process
![]() |
![]() |
Our Factory
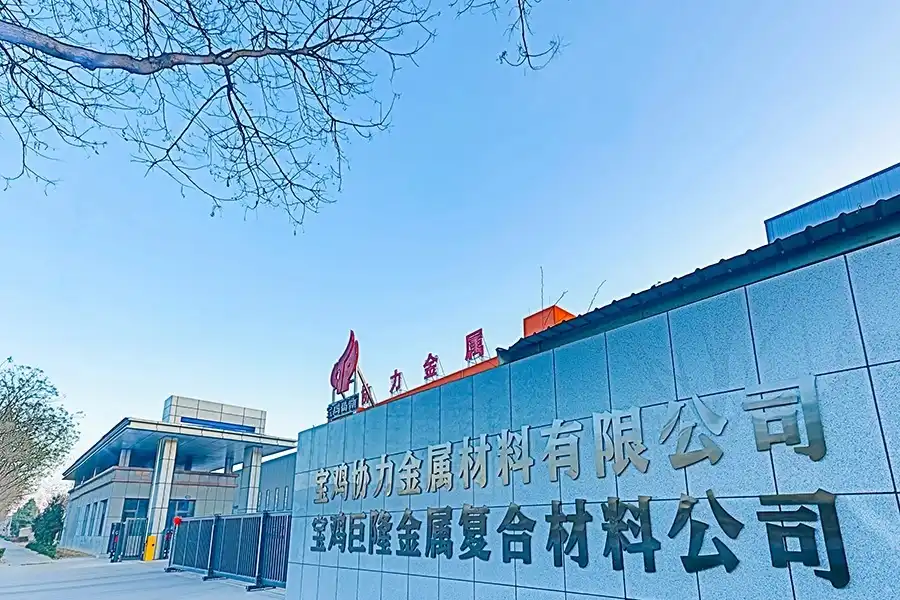
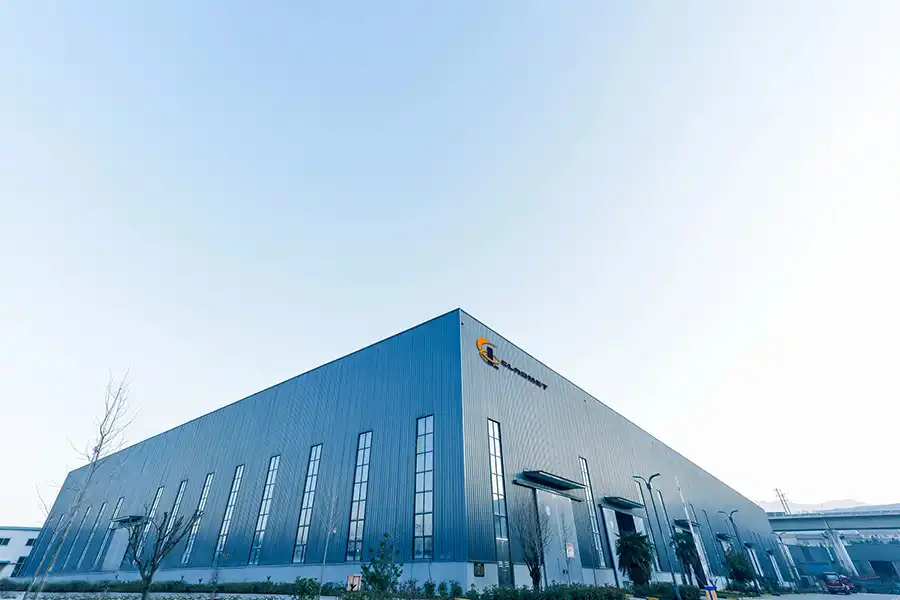
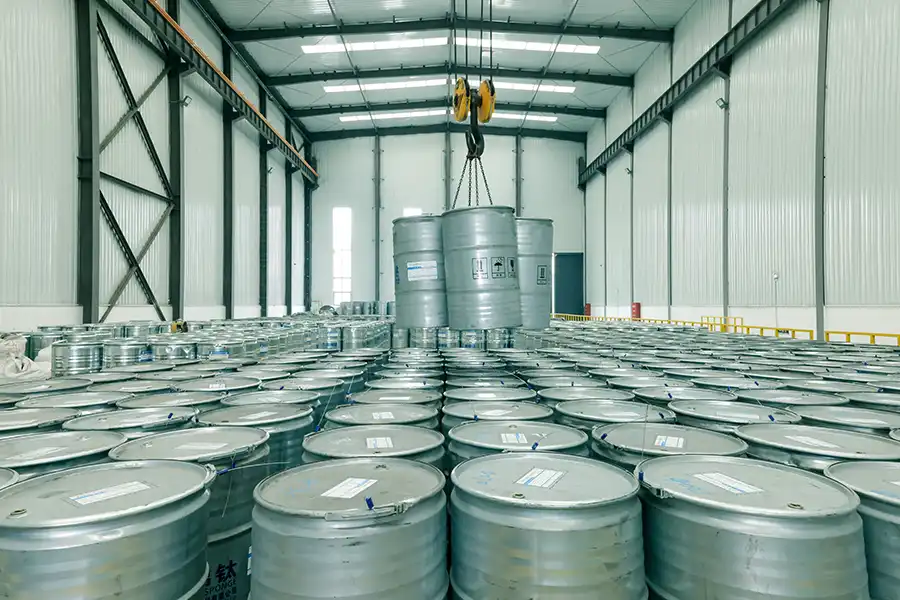
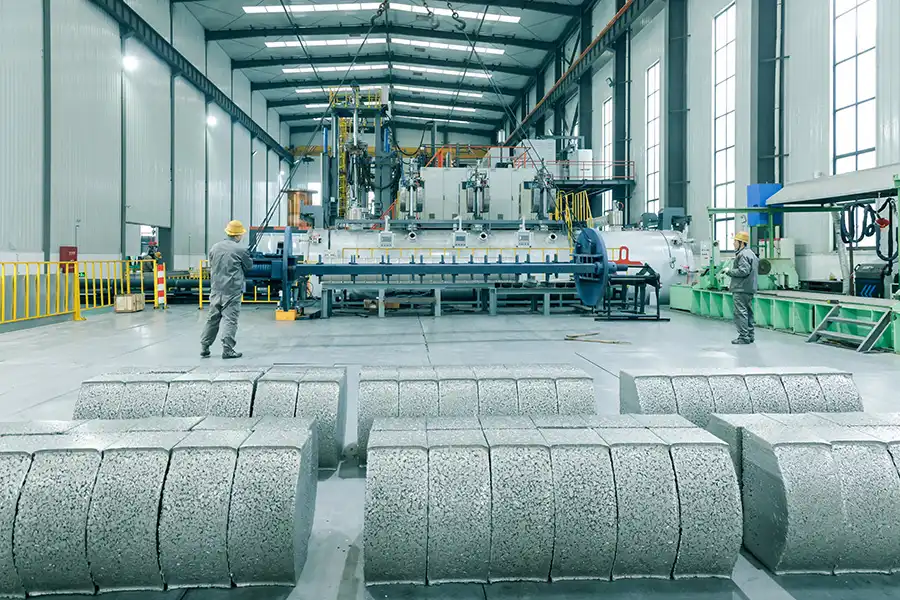
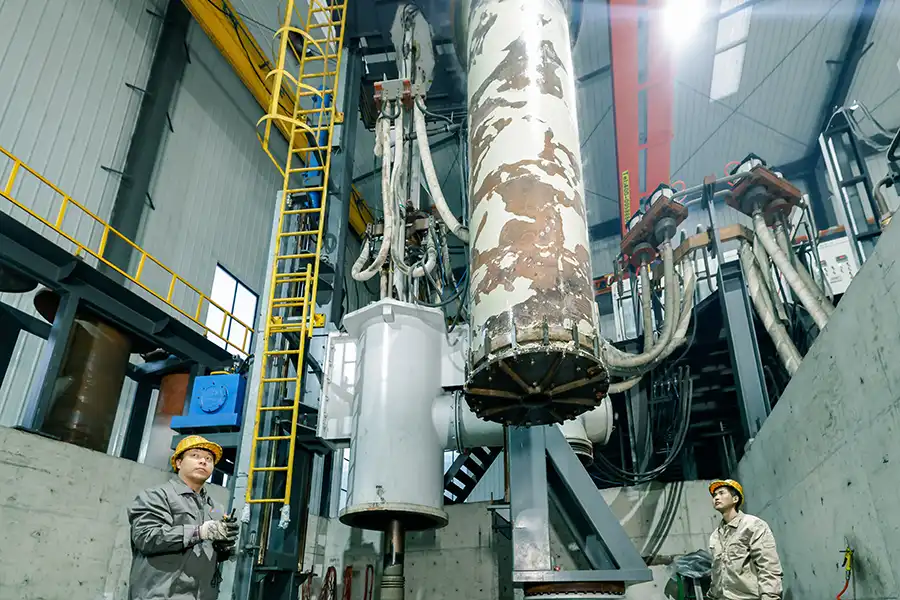
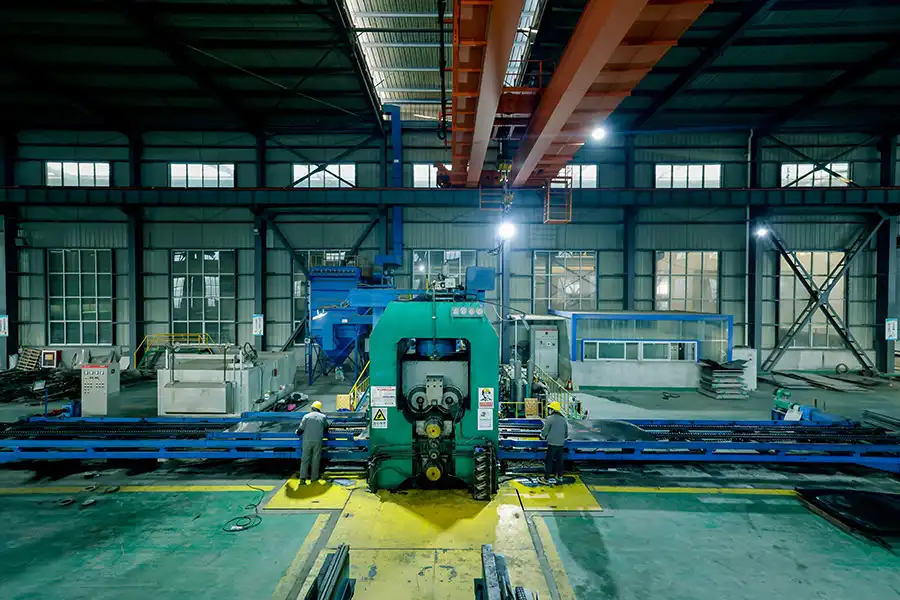
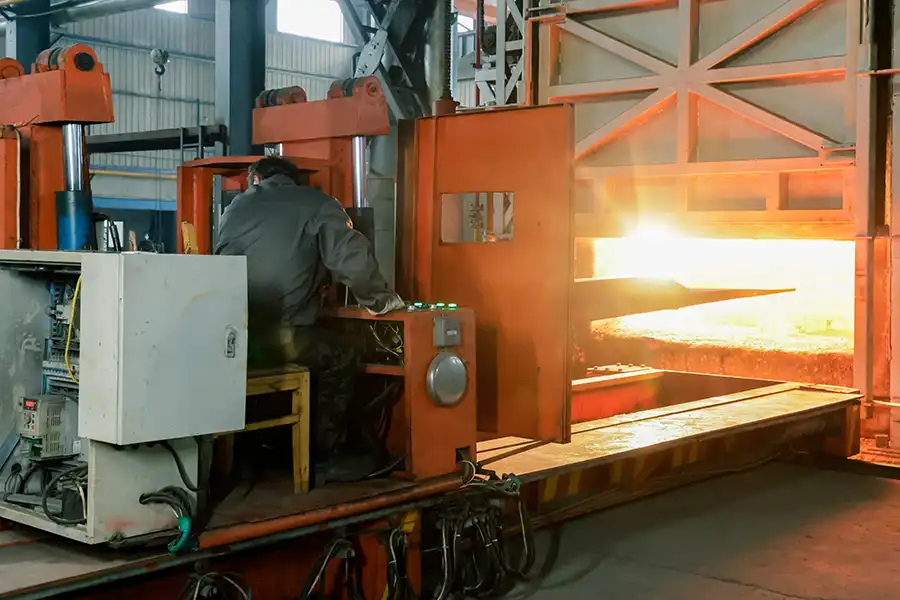
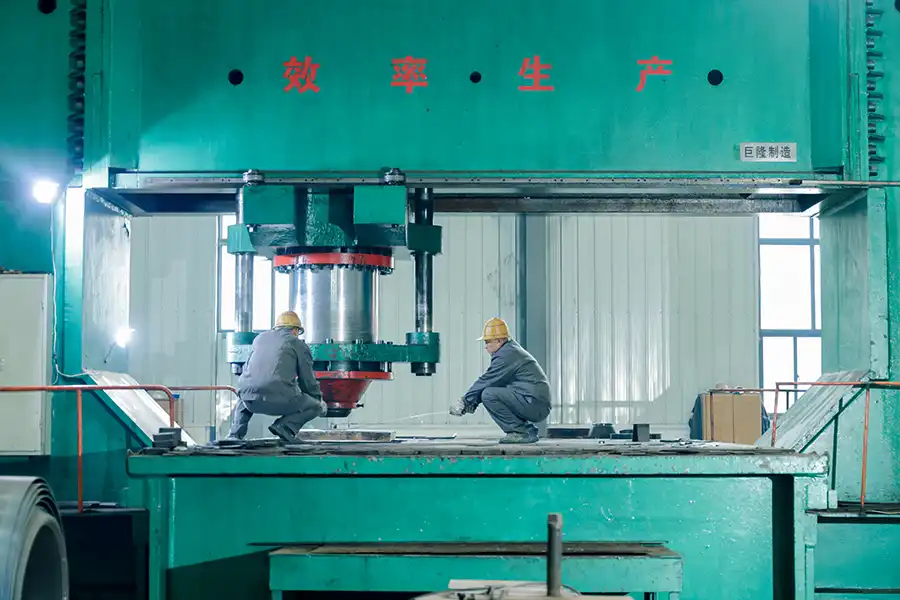
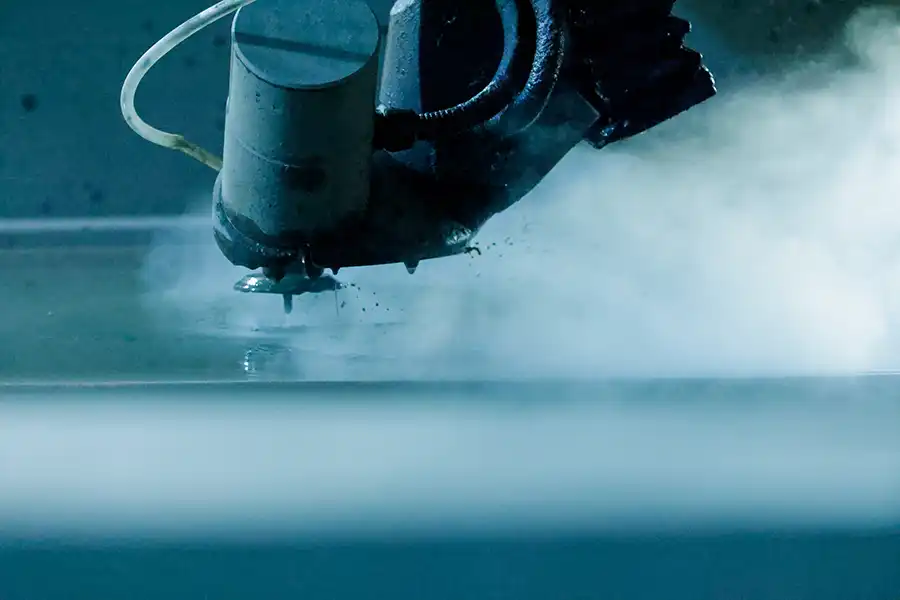
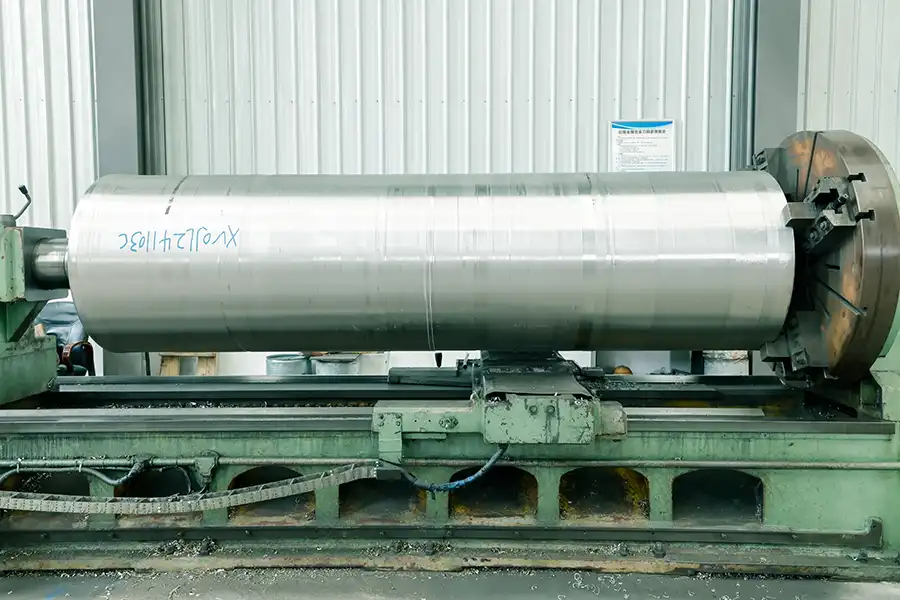
Production Site
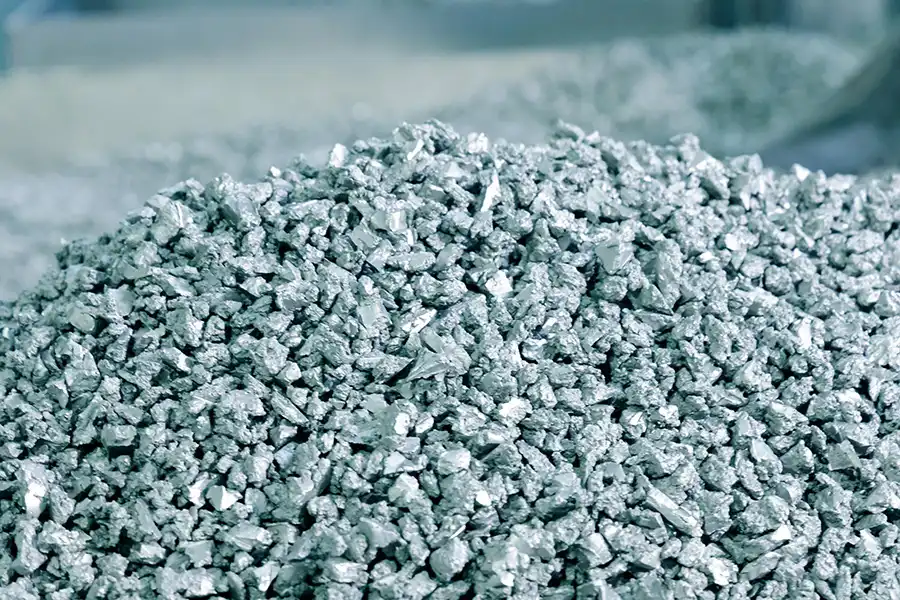
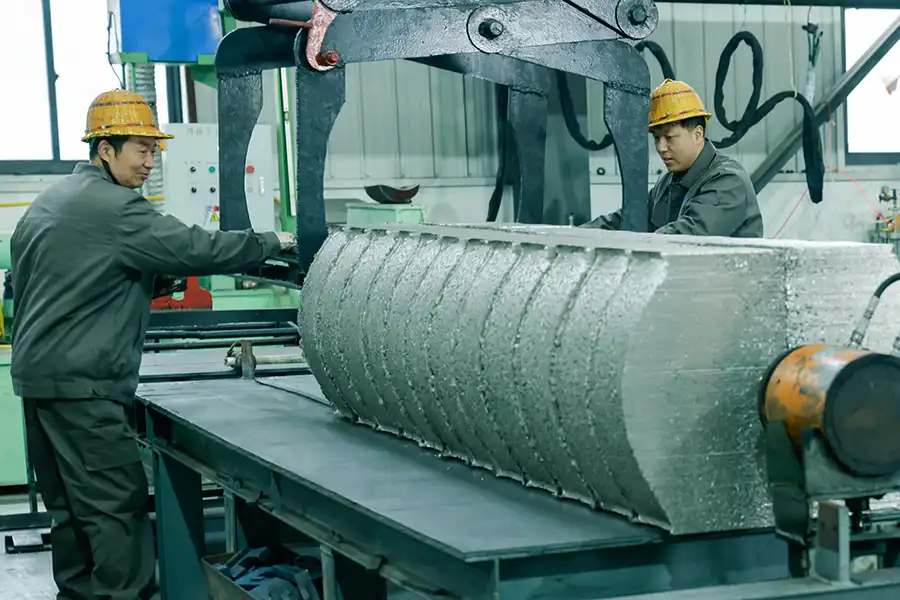
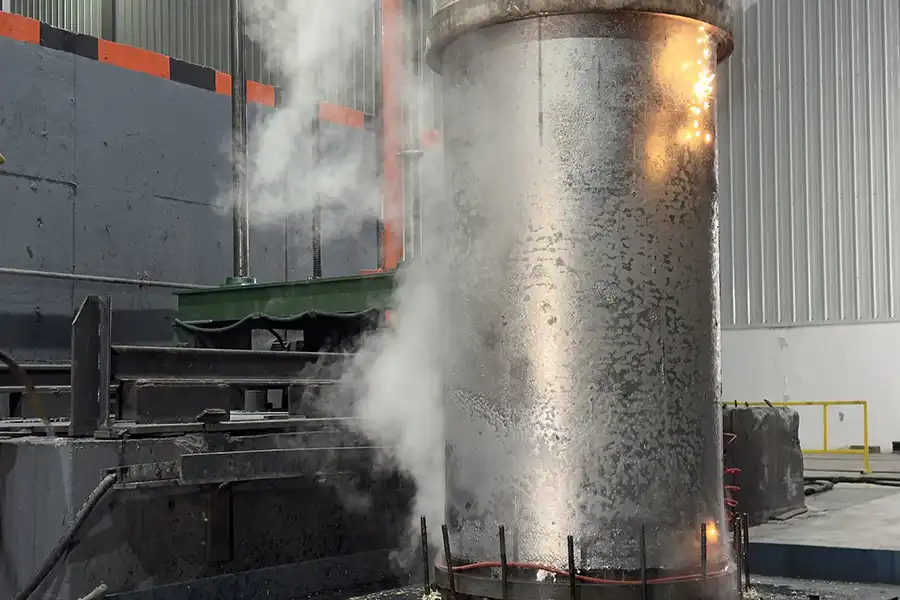

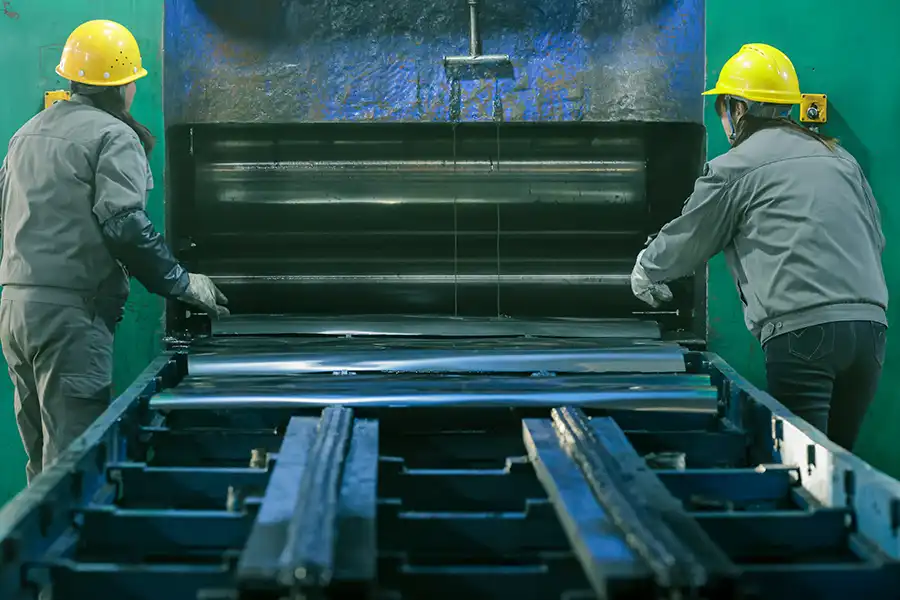
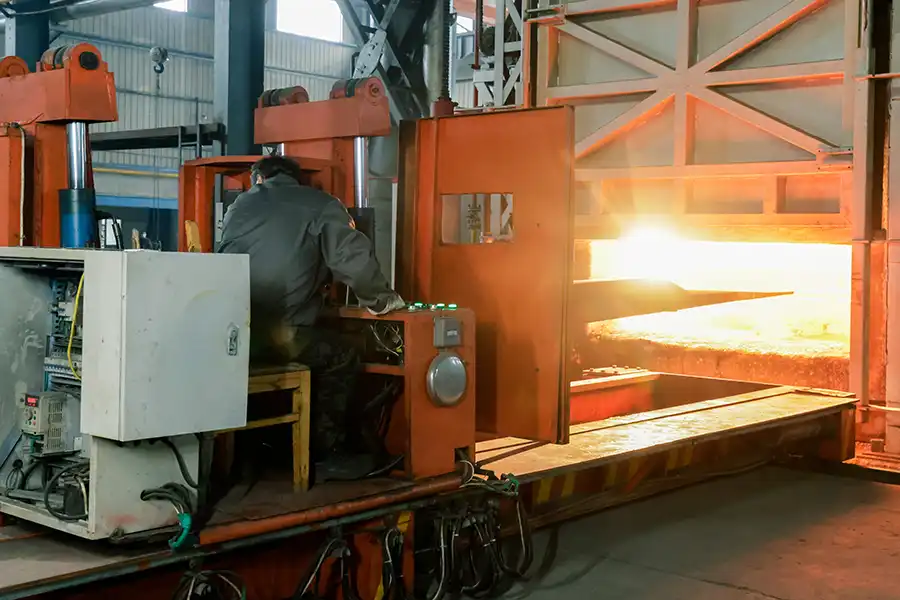
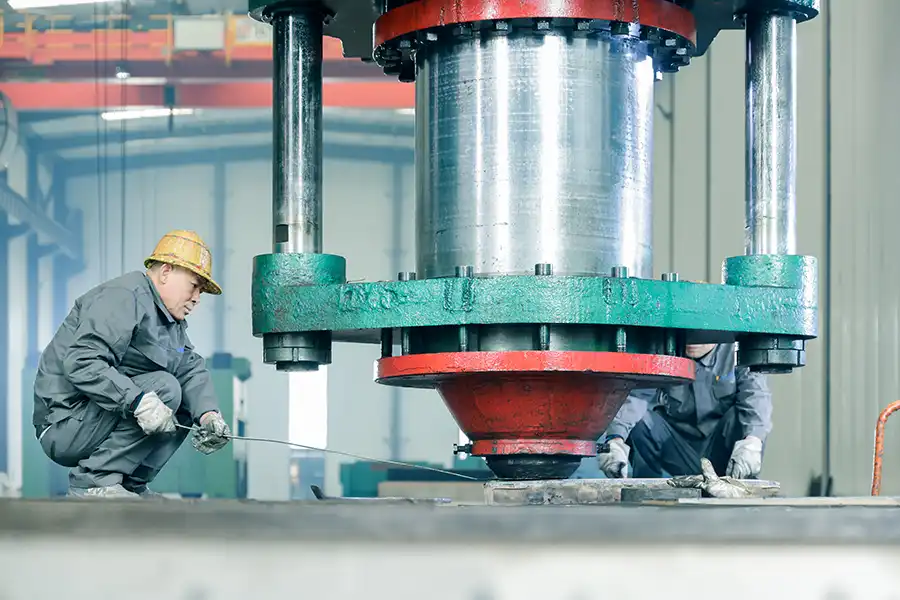
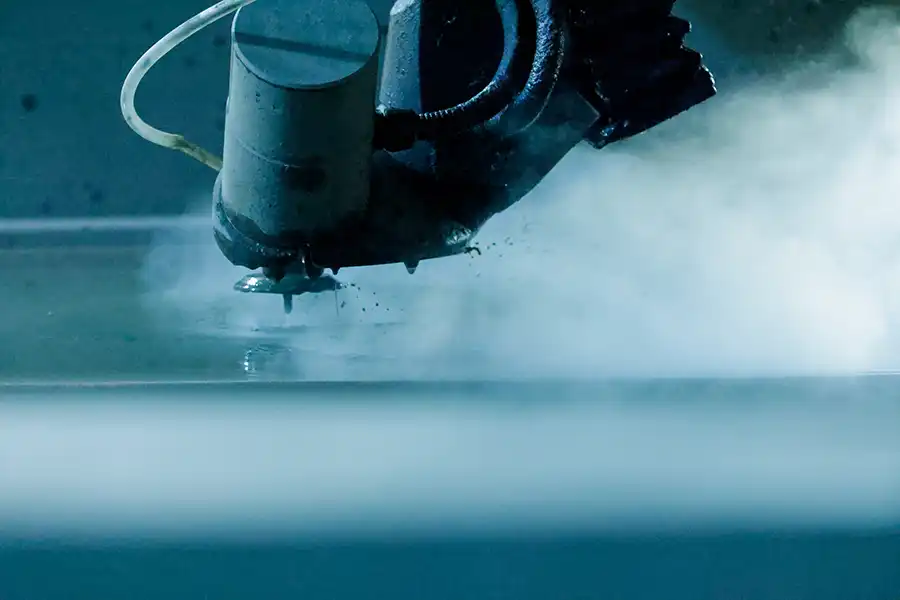
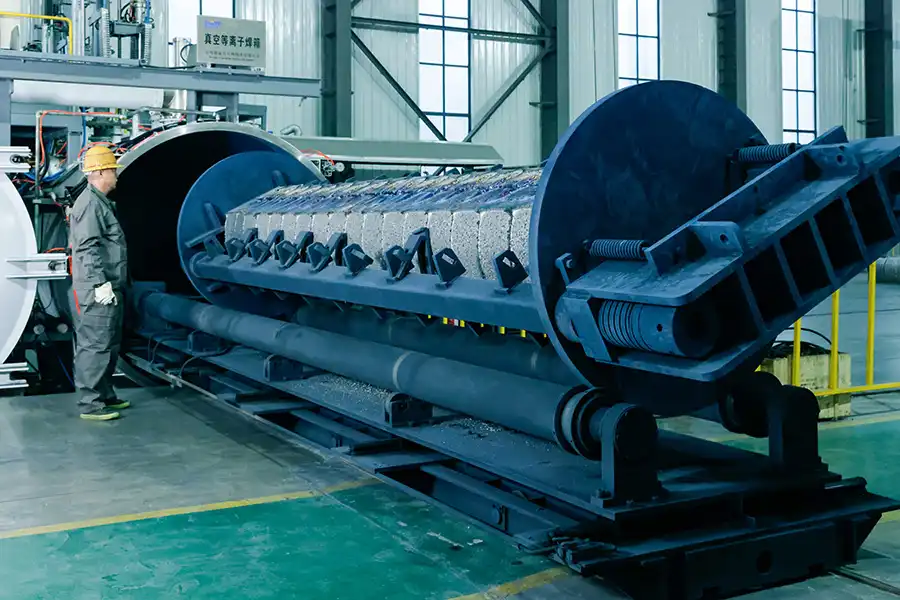

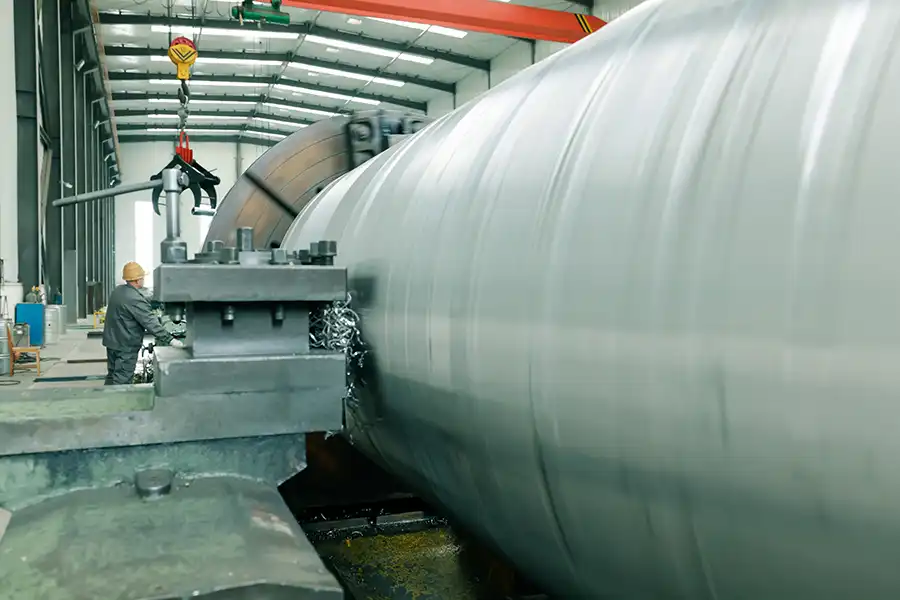
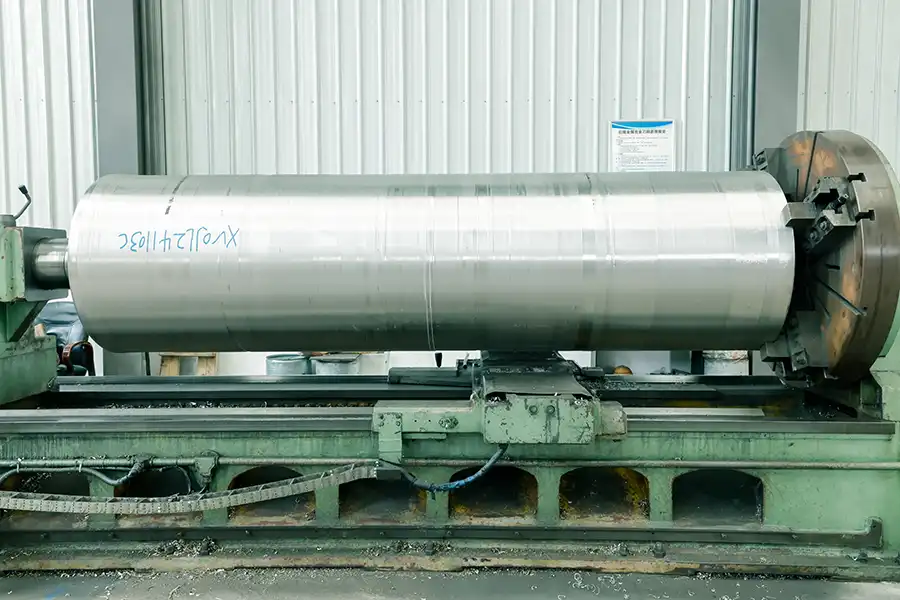
Main Products
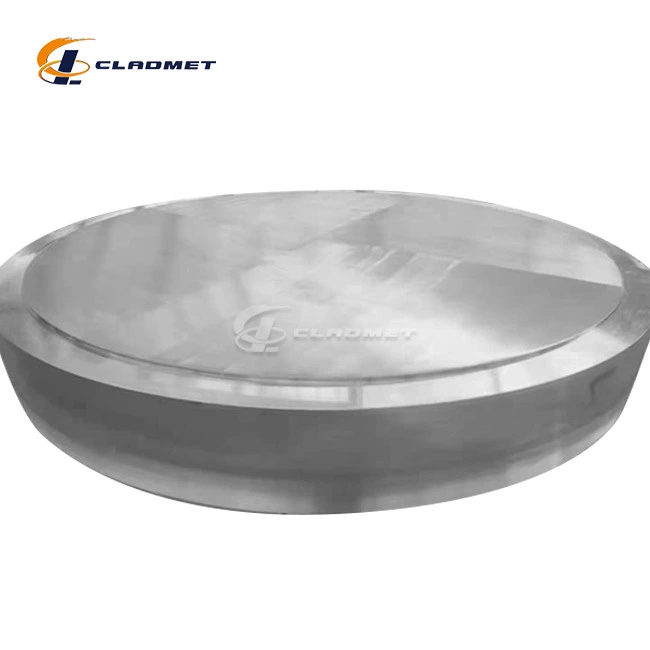
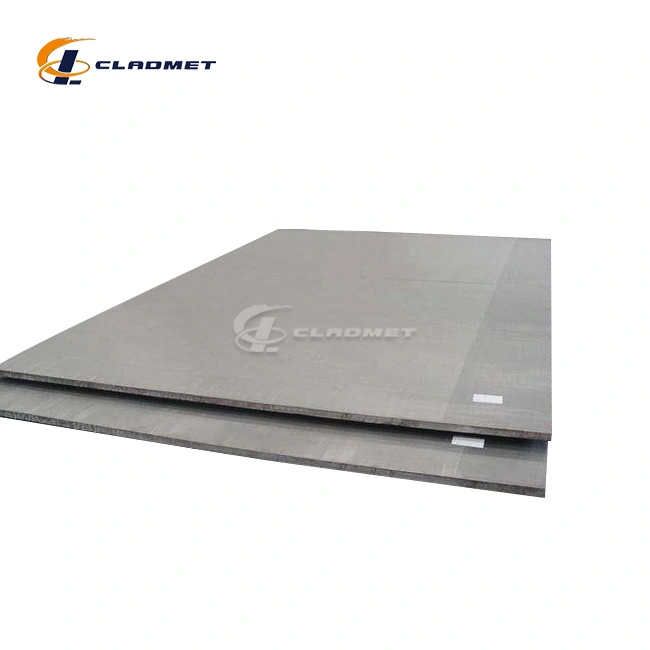
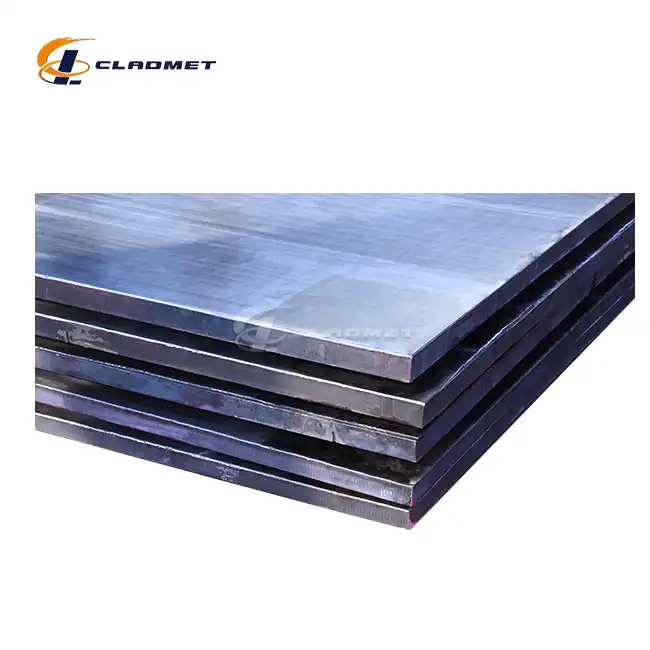
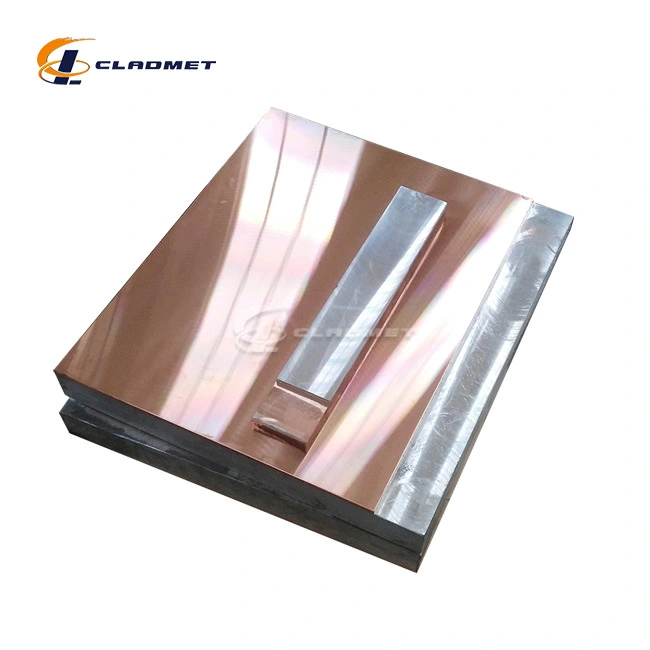
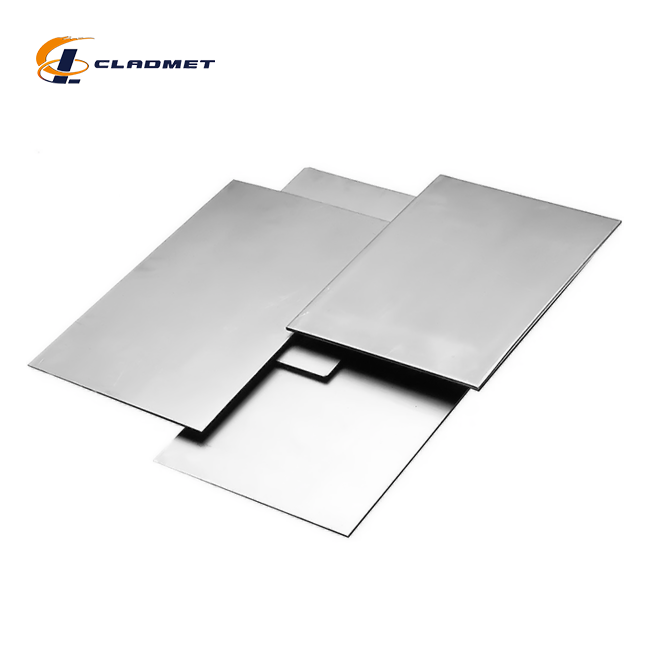
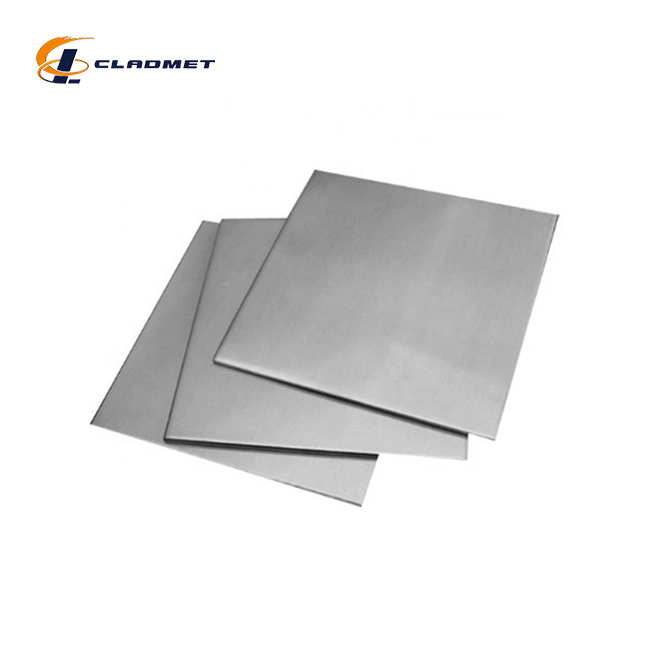
Main Application Industries
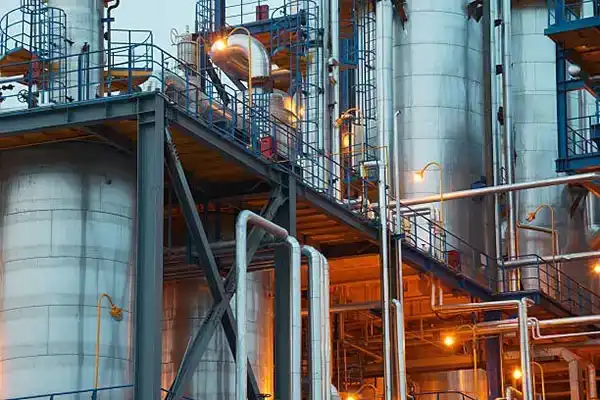
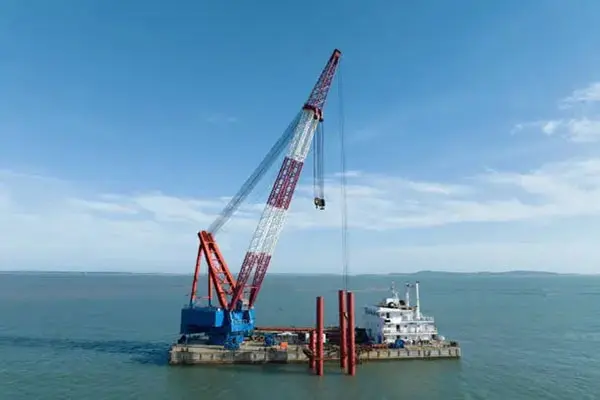
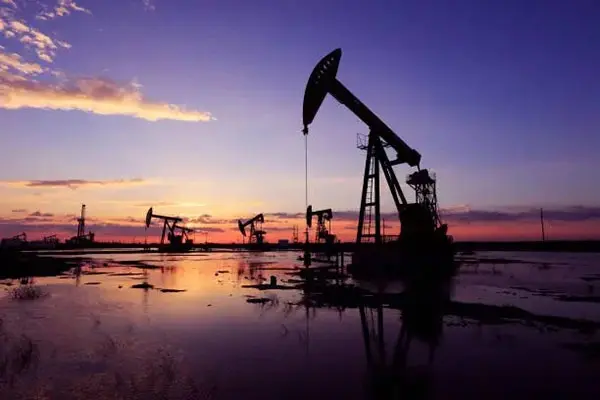
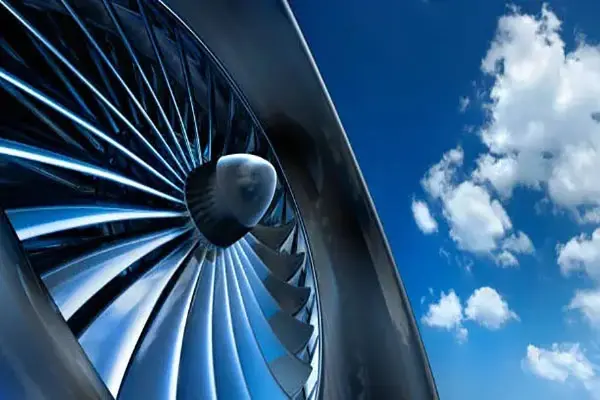
OEM Service
At Baoji JL Clad Metals Materials Co., Ltd., we offer customized OEM services for copper clad aluminum plates. From specific size and material requirements to tailored surface treatments, we work closely with clients to develop solutions that meet their exact needs. Our experienced technical team ensures each product meets international standards for quality and performance.
FAQs
1. What are the advantages of using the product over solid copper?
They provide similar conductivity to solid copper but at a reduced weight and cost, making them more affordable and easier to handle.
2. What is the typical delivery cycle for it?
The delivery cycle is generally 3-6 months, but it can be negotiated based on your specific project needs.
3. Can the plates be customized in terms of size and thickness?
Yes, we offer a wide range of customization options to fit your project's exact requirements.
4. What industries commonly use copper clad aluminum plates?
These plates are widely used in electrical engineering, automotive, aerospace, and marine industries due to their high conductivity and corrosion resistance.
Contact Us
For inquiries and orders, please reach out to us:
- Phone: +86-917-3372918
- WhatsApp: +8613530170059
- Email: sales@cladmet.com
- Address: FENGHUANG 4 ROAD, HIGH-TECH DISTRICT, BAOJI CITY, SHAANXI, CHINA 721013